Manufacturers worldwide are investing heavily in digital transformation, overhauling almost every aspect of their operations and business models. But one key group—frontline workers —are still awaiting their digital renaissance.
Today, many organizations feel their workers are not empowered or digitally well-equipped. Manufacturers struggle with high turnover and the challenge of training and upskilling new workers. Downtime and worker productivity remain nearly universal issues.
To help address these issues, Microsoft is investing in frontline worker enablement across a broad range of technologies. This includes new solutions to help frontline workers deliver exceptional service with next-generation AI, as well as on our ongoing investment in mixed reality hardware and solutions. Microsoft Dynamics 365 Guides cultivates collaborative environments where people put knowledge into action. Here are three ways mixed reality is addressing frontline worker training, support, and knowledge transfer across industries:
1. Resolve issues quickly with remote support and collaboration
Unplanned downtime is costly. The average manufacturer confronts over 800 hours of equipment downtime a year, or 15 hours per week. Industrial manufacturers consequently spend almost USD50 billion on downtime every year.1 In these high-pressure situations, communication across functions can either speed resolution or create blockers to forward progress.
Historically, manufacturing environments fostered knowledge silos with valuable insights confined to individuals, groups, or departments. Mixed reality shifts this dynamic. Workers can share real-time, situational video of their environment, allowing others to experience it firsthand—regardless of location. Expert guidance, troubleshooting, or step-by-step instructions are immediate. This eliminates the need to travel, while minimizing downtime and production disruptions.
Gone are the days where access to experts, communication barriers, or information silos dictate how knowledge is shared or when assets are repaired. Working on assembly or service lines requires specialized skills and expertise. Access to individuals with the relevant, hands-on experience, however, is not always possible. With Dynamics 365 Guides, when specialized skills are required, experts are a Microsoft Teams call away.
Together, Dynamics 365 Guides and Microsoft Dynamics 365 Remote Assist with Teams connect workers beyond their physical limits. A communication hub, Teams enables collaboration across the workforce. Its integration with Dynamics 365 Guides allows workers to extend this to the physical world on any device.
2. Accelerate training with information in context
Frontline workers are the backbone of industry operations. These roles demand technical savvy, quick decision-making, and resiliency. Traditional in-place training and onboarding processes are often ineffective or add to the cognitive burden of overwhelmed frontline workers.
Hands-on training with physical assets is expensive, time-consuming, and at times dangerous. Inconsistent quality or impersonal training is often the result. However, holographic environments can mitigate these on-ramping risks. Embracing mixed reality accelerates learning by introducing relevant, task-specific knowledge in new immersive and data rich environments.
Using 3D models and digital twins, frontline workers receive a better understanding of the machines and processes at hand. Related materials are retrieved or amended instantly, nurturing knowledge exchange, which is further enhanced by AI. Mixed reality is the eyes and ears of AI. Delving into operation nuances for personalized, in-depth learning becomes easier. When integrated, mixed reality and AI accelerate worker training, shortening steps and supplying users with the working knowledge they need for the task at hand.
With Dynamics 365 Guides frontline and service workers can start accelerating their role-based knowledge today. Workers receive purpose-built, interactive guidance on complex machinery, assembly protocols, or maintenance steps when and where they need it.
3. Ensure transfer of information, insights, and skills
As employees near retirement, their wealth of expertise needs to be captured and shared. These experts understand the assets and processes that keep production moving. Retaining and transferring that knowledge is vital. There’s just one problem: Manufacturing is experiencing a talent exodus. Globalization, unemployment, and a rapidly aging workforce together are compounding operational challenges. Organizations are rightfully concerned. One-third of manufacturing executives claim retaining and replacing high-performing employees as a strategic priority in 2023.2 Mixed reality is poised to help solve this by capturing information for informed decision-making and greater productivity.
Mixed reality facilitates knowledge retention and transfer across an organization through the creation of immersive experiences and simulations, regardless of location or device. The versatility of mixed reality makes up-skilling faster and more accessible. Dynamics 365 Guides offers industrial workers the opportunity to document unique situational processes and procedures not included in asset operating manuals. Step-by-step instructions, annotations, and “on the ground” insights are placed in context and immediately accessible throughout the day.
With Dynamics 365 Guides embedded in Microsoft Dynamics 365 Field Service mobile, mixed reality is democratized for every worker. Organizations now have asset, maintenance, and service information at their fingertips. This combination in one app improves worker accuracy, productivity, and efficiency—while offering powerful guidance on the device at hand.
Realize your future manufacturing potential
Mixed reality is a key part of an emerging technology category known as the industrial metaverse. Its foundational cross-platform technologies—including AI, cloud to edge, digital twins, machine learning, and mixed reality—are shifting our relationship with data from stationary to dynamic experiences.
Mixed reality is an essential glue that visualizes the diverse elements of the industrial metaverse. Seamlessly integrating the physical and digital, mixed reality creates immersive experiences that transcend traditional industrial operations. Guides overlays information atop real-world assets and scenarios, making knowledge available in context where it is needed most.
Prepare your workforce for their smart manufacturing future with mixed reality. Learn how Dynamics 365 Guides can help realize tangible business outcomes.
Dynamics 365 Guides
Optimize operations and solve problems in real-time with holographic guidance.
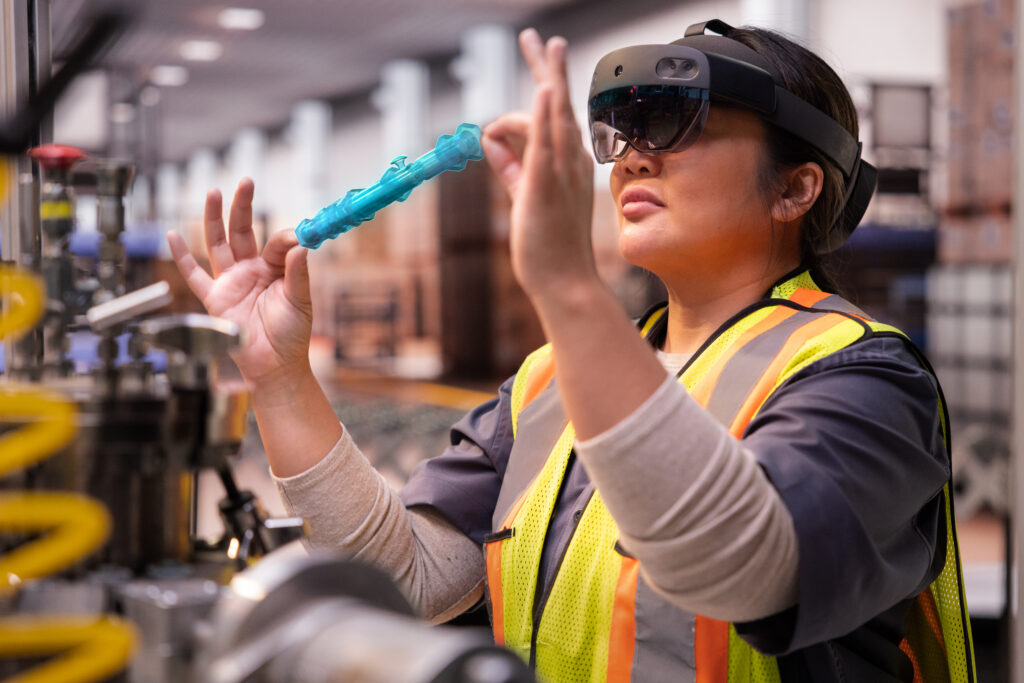
1Manufacturing Without Unplanned Downtime Could Become A Reality Sooner Than You Think, Forbes.